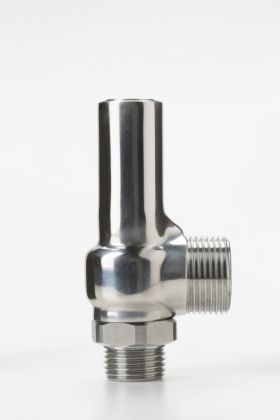
Safety Valve model D10/CS (PN 60)
DN10 (3/8") - DN15 (1/2") | Orifice 10mm
Industries > Cogeneration and Biogas
In the cogeneration and biogas industry, safety is a top priority due to the presence of flammable gases and the risk of potentially explosive atmospheres (ATEX). The equipment installed in these plants must comply with ATEX directives to prevent accidental ignition and ensure safe operation, even in critical conditions.
All equipment for cogeneration and biogas applications must ensure maximum resistance to corrosion, the ability to handle high pressures, and compatibility with biogas. Therefore, it is necessary to:
Hydrogen present in biogas as H2S is an extremely volatile gas with a high diffusion rate, making it essential to adopt solutions that guarantee a perfect tightness. Given the potential presence of ATEX explosive atmospheres, the complete hermetic sealing of the plant is an imperative aspect in the cogeneration and biogas industry.
In cogeneration systems and biogas plants, safety valves are often installed after compressors to ensure the safe disposal of the flow generated by these components in case of malfunctions, failures, or emergency situations such as external fires that lead to uncontrolled pressure increases.
Compressors, during their operation, can generate very high pressures, and if these are not properly managed, they could cause damage to the plant or jeopardize operational safety. Safety valves are positioned at the compressor outlets to "vent" excess pressure and prevent structural damage or the risk of explosions. In the event of a malfunction or failure, such as a component rupture or system blockage, the valves automatically activate to divert the excess flow, protecting the system from potential pressure overloads. Furthermore, in case of an external fire, the valves help prevent damage caused by overheating or excessive pressurization by releasing the gas in a controlled and safe manner. This timely intervention is critical to ensure the plant's safety and the safe operation of the entire system.
The presence of flammable gases and the risk of potentially explosive atmospheres (ATEX) requires the use of safety valves designed with materials and construction solutions suitable to prevent static charge buildup, gas leakage, and overheating, while ensuring optimal efficiency throughout the system.
Nuova General safety valves can be supplied with ATEX certification (second category equipment), making the product suitable for ATEX zones 1, 2, 21, and 22. During the full opening of the valve, the movement of the shutter can generate mechanical sparks.
To eliminate this risk, we have made specific technical modifications to the product. These adjustments are detailed in the technical datasheet provided to the official certification body for ATEX.
When the operating pressure approaches the set pressure of the safety valve, even minimal variations due to temperature fluctuations or load changes can cause undesired discharges. This phenomenon can lead to the release of methane, H2S, or other dangerous gases, increasing energy consumption, reducing system efficiency, and raising operational costs. Furthermore, unnecessary valve activations can compromise plant stability and cause critical malfunctions.
To prevent unwanted activations, our safety valves are calibrated with a positive margin of +3% above the nominal set pressure, in accordance with ISO 4126, ASME, and PED standards. This measure offers two key advantages:
To ensure maximum reliability, all Nuova General safety valves for cogeneration and biogas applications are subjected to tightness tests at 90% of the set pressure, using a nitrogen and hydrogen mixture (95% N2 - 5% H2). Certified sniffers are used to verify the complete absence of hydrogen leaks, ensuring compliance with the strictest regulations and guaranteeing safe and efficient operation over time.
For cogeneration and biogas plants, it is essential that the valves are constructed with certified, corrosion-resistant materials suitable for high pressures.
Our safety valves are made with 100% Italian materials, ensuring full traceability and the highest quality. All components are selected to withstand the extreme environments typical of cogeneration and biogas, where high pressure, aggressive gases, and severe operating conditions demand reliable and durable solutions.
The use of 316L stainless steel, highly resistant to corrosion, ensures optimal performance even in the presence of hydrogen, aggressive chemicals, or extreme temperatures. Furthermore, for pressure parts, we can provide a material certificate 3.1 upon request, confirming compliance with the strictest quality standards.
Each valve undergoes rigorous testing at 1.5 times the design pressure, verifying its ability to operate safely even at high pressures, ensuring maximum reliability over time.
The ASME (American Society of Mechanical Engineers) certification is crucial to ensure the quality and safety of equipment subjected to high pressures, such as safety valves used in cogeneration and biogas applications. This certification attests that the valves meet international standards for design, manufacturing, and testing, ensuring they can operate in extreme conditions without compromising safety. The ASME certification is particularly relevant for ensuring the strength and reliability of components in critical operating environments, minimizing the risk of structural failures.
The ATEX certification is essential to ensure that safety valves and equipment used in cogeneration and biogas industries are safe for use in potentially explosive environments. ATEX (Atmosphères Explosibles) sets the requirements for devices and systems operating in areas where there is a risk of explosions due to the presence of gases, vapors, or combustible dust. The certification ensures that equipment is designed, tested, and manufactured to prevent risks, offering protection against dangerous events and enhancing the operational safety of the plants.
DN10 (3/8") - DN15 (1/2") | Orifice 10mm
DN15 (1/2") - DN20 (3/4") - DN25 (1") | Orifice 13,5mm
DN20 (3/4") - DN25 (1") | Orifice 20mm
DN32 (1"1/4) - DN40 (1"1/2) | Orifice 25mm
DN15 (1/2") - DN20 (3/4") | Orifice 10mm
DN15 (1/2") - DN20 (3/4") - DN25 (1") | Orifice 10mm
DN15 (1/2") - DN20 (3/4") - DN25 (1") | Orifice 5mm
DN15 (1/2") - DN20 (3/4") - DN25 (1") | Orifice 8mm
Choosing a Nuova General Instruments safety valve means relying on a product designed and manufactured according to the highest quality and safety standards. In addition to our years of experience and continuous focus on innovation, we offer a range of dedicated services to support our customers at every stage, from product selection to after-sales assistance:
• ⚡ Fast Delivery: Standard production within 10 business days, with a Fast Track option for shipments in just 5 days.
• 📦 Flexible Lot Sizes: We provide both single valves and large batches up to 1000 units, always ensuring top quality.
• 🎨 Customization: Laser marking, colored caps for calibration identification, and removable barcode labels for simplified management.
• ✅ Third-Party Testing: Option to obtain 3.2 test certificates from prestigious organizations such as INAIL, TUV, RINA, LLOYD, DNV, and ABS.
• 📄 Online Certificates: Immediate and unlimited access to technical documentation of the valves through our dedicated portal.
• 🛠️ Product Samples: Ability to test our valves before placing regular orders, with specialized technical support.