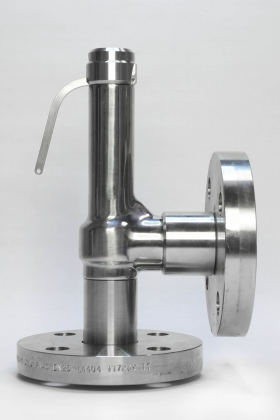
Safety Valve model G14/L (PN 60)
DN15 (1/2") - DN20 (3/4") - DN25 (1") | Orifice 13,5mm
Industries > Steam Generator and Boilers
In safety valves installed on steam generators, high temperatures are a critical factor affecting both performance and component longevity. These conditions lead to:
A key standard in this sector concerns flanged connections, ensuring a strong and reliable valve attachment to the system.
In Europe, UNI EN 1092-1 flanges are used, classified by nominal pressure (PN), while in American or international plants, ANSI flanges are adopted, categorized into classes (150, 300, 600, etc.). The choice depends on the plant specifications and market requirements, ensuring compatibility and regulatory compliance.
In the steam generator industry, safety valves (PSVs) are installed directly on the generator to monitor and control internal pressure.
When the pressure exceeds the preset safety limit, the PSV opens to release excess steam, preventing system damage. In this configuration, the valve is in constant contact with steam, requiring materials resistant to high temperatures and thermal stress conditions. This ensures reliable and safe operation, minimizing the risk of deterioration or malfunctions caused by direct exposure to superheated steam.
High temperatures in steam generators are a critical factor in selecting safety valves, as they affect component performance and durability. It is essential that valves are designed to operate reliably even in extreme conditions, ensuring proper response and compliance with safety regulations.
Nuova General Instruments' safety valves for steam are calibrated directly on a steam generator to replicate the final application as accurately as possible. This ensures the proper functioning of this critical safety component even under high temperatures.
Our valves are made with 100% Italian materials, ensuring full traceability and superior quality. Depending on the set pressure and operating temperature, components are manufactured in brass or 316L stainless steel, guaranteeing optimal safety valve (PSV) performance.
To ensure long-term reliability, we use high-performance soft seals designed to maintain a tight closure even after each valve activation. This minimizes the risk of leaks, ensuring maximum system safety.
Flanges are essential connections for steam generators, providing sealing and stability. However, their positioning can be challenging, especially when aligning the valve outlet with the system piping. Improper alignment can compromise system efficiency and lead to malfunctions in steam discharge.
Our flanged safety valves feature a collar flange at the inlet, offering significant installation advantages. In this design, the valve body remains fixed while the flange can rotate, allowing precise and easy orientation of the valve to fit the system piping perfectly.
With this rotating flange system, aligning the PSV with the piping requires minimal effort, reducing installation time and difficulty while ensuring optimal configuration for safe and efficient operation.
Steam generators operate continuously, making regular maintenance of safety valves challenging. Disassembling and inspecting a valve requires shutting down the system, a procedure that can be complex and costly as it directly impacts production.
Natioanl Standards regulates the installation, operation, and periodic inspection of pressure equipment, including safety valves on steam generators. The NoBo usually requires these valves to be tested and inspected every two years to ensure proper operation and regulatory compliance. However, since these systems operate continuously, scheduling inspections without disrupting production is a challenge.
If safety valves are not regularly inspected, the system may fail to comply with regulations, leading to potential fines or operational suspension. Companies must adopt solutions that ensure compliance without compromising efficiency.
To minimize downtime and ensure compliance with regulations, we offer a retesting and reconditioning service for safety valves, keeping them certified according to the applicable safety standards.
To maintain operational continuity, we support our customers with the backup valve system. This involves purchasing two identical valves (e.g., Valve A and Valve B). While Valve A is installed in the system, Valve B is sent to us for retesting and certification. At the time of inspection, the customer can quickly replace Valve A with the certified Valve B, avoiding downtime and ensuring the system always operates with a compliant valve.
In this way during plant inspections, the valve will already be tested, certified, and accompanied by the certification, simplifying the control process and ensuring maximum safety.
In Italy, industrial plants must often be tested by third-party organizations, such as INAIL, to ensure compliance with current regulations. Safety valves and pressure equipment require certifications and periodic inspections to guarantee adherence to safety standards, reduce the risk of accidents, and ensure the proper operation of the systems.
In European plants and projects adopting CE standards, compliance with European regulations is mandatory, particularly with the PED (Pressure Equipment Directive) for pressure equipment and specific regulations for process piping. This compliance ensures high standards of operational safety and structural quality.
DN15 (1/2") - DN20 (3/4") - DN25 (1") | Orifice 13,5mm
DN20 (3/4") - DN25 (1") - DN32 (1"1/4) | Orifice 20mm
DN25 (1") - DN32 (1"1/4) - DN40 (1"1/2) | Orifice 25mm
DN32 (1"1/4) - DN40 (1"1/2) | Orifice 32mm
DN40 (1"1/2) - DN50 (2") - DN65 (2"1/2) | Orifice 38mm
DN40 (1"1/2) - DN50 (2") - DN65 (2"1/2) | Orifice 40mm
Choosing a Nuova General Instruments safety valve means relying on a product designed and manufactured according to the highest quality and safety standards. In addition to our years of experience and continuous focus on innovation, we offer a range of dedicated services to support our customers at every stage, from product selection to after-sales assistance:
• ⚡ Fast Delivery: Standard production within 10 business days, with a Fast Track option for shipments in just 5 days.
• 📦 Flexible Lot Sizes: We provide both single valves and large batches up to 1000 units, always ensuring top quality.
• 🎨 Customization: Laser marking, colored caps for calibration identification, and removable barcode labels for simplified management.
• ✅ Third-Party Testing: Option to obtain 3.2 test certificates from prestigious organizations such as INAIL, TUV, RINA, LLOYD, DNV, and ABS.
• 📄 Online Certificates: Immediate and unlimited access to technical documentation of the valves through our dedicated portal.
• 🛠️ Product Samples: Ability to test our valves before placing regular orders, with specialized technical support.